Forum for students doing their Diploma in Childcare.
Forum rules
IMPORTANT: Student's support in our forum will now be a part of our Premium Subscription service. This means students who have purchased a Premium Subscription will now be offered complimentary support in our Student Forums by us. This will only be available to students who have purchased a Premium Subscription. Click here to subscribe.
-
Educater
- Participator
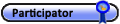
- Posts: 20
- Joined: Sat Jun 18, 2011 9:42 pm
Post
by Educater » Mon Jun 20, 2011 3:20 pm
hi everyone i need a bit of jelp with some of my questions...i'd really appreciate your answers on this ..Thanks a lot in advance
Question 1
identify a hazard which has been managed using a "Hierarchy of control" method. Explain?????
Question 2
what strategies are used at your service to identify hazard that exist in the care environment???? provide example????
plz plz plz reply as soon as possible..waitinggggg impatiently for your replies..

Last edited by
Lorina on Sat Aug 23, 2014 5:27 am, edited 2 times in total.
Reason: topic heading has been edited
-
Lorina
- Moderator
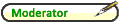
- Posts: 14399
- Joined: Thu Nov 19, 2009 7:36 am
Post
by Lorina » Mon Jun 20, 2011 6:42 pm
Hi Nida,
Welcome to Aussie Childcare Network!
Just got home from work and ready to start helping you out with your assignment question
!
identify a hazard which has been managed using a "Hierarchy of control" method. Explain?????
The Hierarchy of Control is a list of control measures, in priority order, that can be used to eliminate or minimise exposure to the hazard.It consists of two levels.
LEVEL 1
1st Priority - Elimination of Hazard: The best way to eliminate the risk is to completely remove the hazard. For e.g. the need for excessive photocopying and collation can be eliminated if material is circulated by electronic mail; repair damaged equipment promptly; ensure new equipment meets the ergonomic needs of users; move a noisy machine from a quiet area.
LEVEL 2
2nd Priority - Substitution -Replacing a hazardous substance or work practice with a less hazardous one. For e.g. a telephone hand set can be replaced with a head set where there is constant use of the telephone, substituting a smaller package or container to reduce the risk of manual handling injuries such as back strain, substituting a hazardous chemical with a less dangerous one
3rd Priority - Engineering - The provision of mechanical aids, barriers, machine guarding, ventilation or insulation to isolate a hazard from employees. For e.g. electrical cut out switches, roll over frames on vehicles, duress alarms or mechanical screens to separate workers from violent or physically aggressive clients, isolating copying equipment in soundproof and ventilated rooms, using anti-glare screens on computers, using trolleys or mechanical lifting aids, changing bench heights to reduce bending.
4th Priority - Administration - Establishing policies, procedures and work practices designed to reduce a worker’s exposure to a risk. It can also include the provision of specific training and supervision.For e.g. providing alternative tasks for workers so as to prevent continuous keyboard work for long periods, increasing job variety and introducing job rotation, redesigning jobs, regularly maintaining plant and equipment, training and education on legislative and OH&S issues.
Last Priority - P.P.E. - Personal Protective Equipment - Covering and protecting a worker’s body from hazards. It can be used as a short-term control measure until a “higher order” control has been provided, or to supplement it. For e.g. ear plugs in noisy areas, eye protection when working with chemicals, gloves to protect against infection.
It's best to start at Level 1 and try and eliminate the hazard that has been identified. However, if the hazard cannot be eliminated then move onto level 2 and put in place one of the control measures.
I got the above info from the following link: http://www.saunions.org.au/ohs/hierachy ... limination
what strategies are used at your service to identify hazard that exist in the care environment???? provide example????
- Indoor Safety Checklist
- Outdoor Safety Checklist
- Risk Management Documentation
- Policies and Procedures
- OH&S Training and Consultation
- Incident/Accident Reports
Take a look at the following pdf document that can provide you with examples you may need. Click here to read more.
This should get you started... please share if you find out any more info!
,
L.A
-
Educater
- Participator
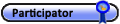
- Posts: 20
- Joined: Sat Jun 18, 2011 9:42 pm
Post
by Educater » Tue Jun 21, 2011 11:01 am
thanks a lot L.A thats exactly what i nedded and sort of wasnt sure what to do...u r a really great helper ...thanksssss so much ...may god always keep u happy and well